Abstract
Restricted to the physical properties of pure copper, copper is usually manufactured into copper alloy forms by adding small amounts of silicon, nickel, tin, zinc, chromium or silver, in order to enhance the ability of resistance of copper to surface cracking, porosity problems and avoid the formation of internal cavities etc.However, to cast these alloys with different substances added, the required casting techniques differed. As technology develops, there are more and more approaches to process copper and copper alloy. Copper and copper alloy casting methods manufacturers adopt nowadays are various, the existing casting methods can be roughly classified into six major types, including
- Centrifugal Casting
- Shell Molded Casting
- Chill Casting
- Die Casting
- Sand Casting and CO2 Process
- Continuous Casting
The further explanation of each casting skill is covered in the following paragraphs.
Contents
- Centrifugal Casting
- Shell Molded Casting
- Chill Casting
- Die Casting
- Sand Casting and CO2 Process
- Continuous Casting
- Strengths of HSIN HUAN LUNG MACHINERY INDUSTRIAL COMPANY (HHL)
Centrifugal Casting
Centrifugal casting, also referred as Liquid Forgings, is a casting technique that utilizes centrifugal forces. During the high-speed rotation enforced by a centrifugal casting machine, the substances within the material disperse to different layers based on the density due to the high compressive pressure.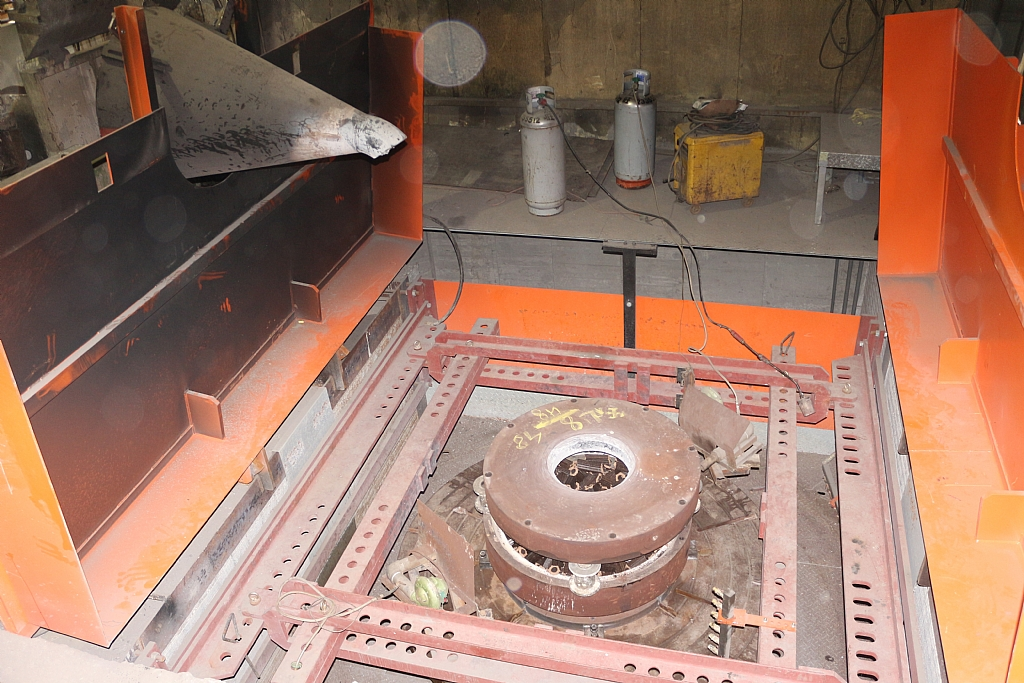
Vertical Centrifugal Machine
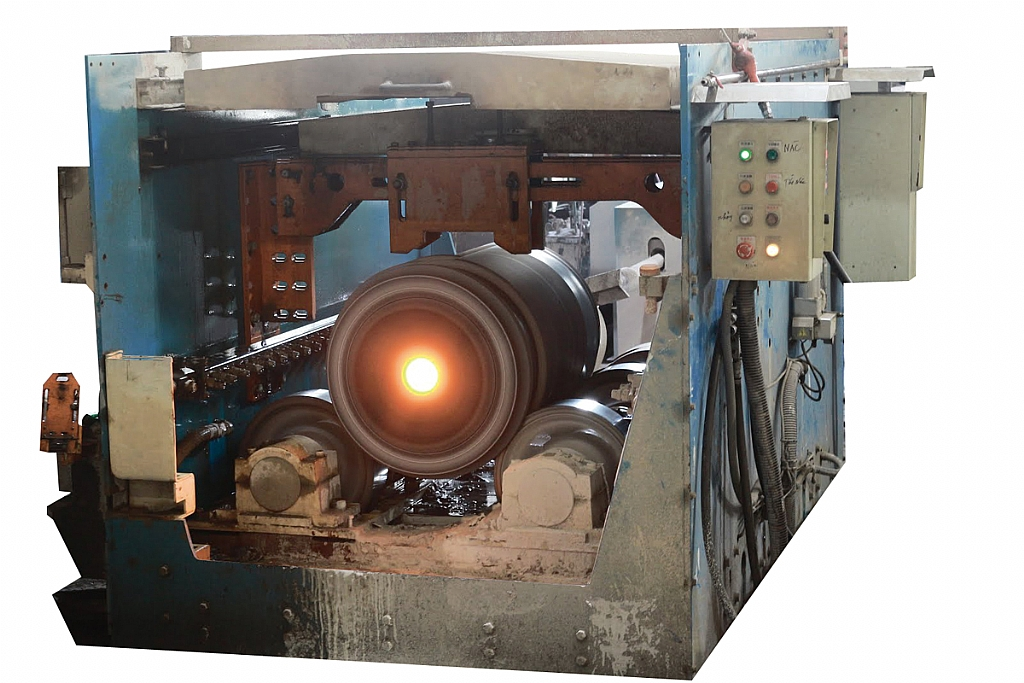
Horizontal Centrifugal Machine
Centrifugal casting fits almost all of copper alloy, what is more, centrifugal casting is relatively affordable in contrast to the other casting techniques. However, centrifugal casting is usually rough machined, which may cause higher general tolerances, in addition, surface finish is not applicable.
When it comes to the size range of centrifugal-casted production, depending on foundry capacity, sizes ranging from an ounce to 25,000 pounds. Minimum section thickness is a quarter of an inch.
▶ More information about Centrifugal Casting
Shell Molded Casting
Shell molded casting is a machine molding process employing synthetic thermosetting resin mixed with high grade silica sand. Been developed in the last 50 years, shell molded casting is capable of composing all kinds of copper alloy in very much closer tolerances while in mass production.Shell molded casting has been praised at the ability to improve the quality of surface finish and definition obtainable magnificently that it is possible to keep the tolerances on certain dimensions of the order of 0.003 inch. Nonetheless, shell molded casting is usually more costly to produce for plate molding and sand casting, due to the accuracy it can achieve and the implicit cost from resin and high grade sand.
Under most conditions, machining operations and machining allowances can be significantly cut if shell molded castings are applied. Therefore, shell molded casting shows great advantages over other methods of production in producing components, especially in the production of lightweight metal.
Chill Casting
Chill casting is majorly applied on tin bronzes, such as phosphor bronze, gunmetal, leaded bronze and leaded gunmetal. By the application of chill casting, manufacturers are capable of composing components weighing from a few ounces up to hundredweights, including chill cast sticks, rods and other irregular shapes.As you may tell from the name, this technique can help to speed up the solidification of the process, which benefits the general quality and the hardness figures of the outcomes. What’s more, all mechanical properties of the outcome except the elongation and reduction of area, are able to be boosted by chill casting.
Die Casting
Die casting, also addressed as Gravity Die Casting, is a conventional casting technique. Generally applied in non-ferrous metals and alloys, die casting is especially suitable for aluminum bronzes and tensile brasses. Die-castings have numerous advantages, namely outstanding surface finish, high dimensional accuracy and excellent mechanical properties for instance.To step further, the combination of distinctive surface finish and close dimensional accuracy leads to the reduction or complete elimination of machining, however, castings of complicated shapes may increase the difficulty to the foundry worker for unsoundness out of the alternate thick and thin sections aggravate feeding problems, or the difficulty to remove from the die.
Sand Casting and CO2 Process
Sand casting is also a traditional casting technique for copper and alloy. The main advantage of sand casting is the ability to produce unique shapes that are not obtainable through other casting processes derived from the maturity of the technique.Casting processes subordinate to sand casting including CO2 process, furan resin sand casting, and green sand molding. Among the subordinate processes, the CO2 process possesses a great potential to replace dry sand molding and a large proportion of green sand molding, due to its greater accuracy.
Continuous Casting
Continuous casting is a relatively new casting technique than all the other techniques we mentioned, usually applied in processing tin bronzes, phosphor bronze, leaded bronze, gunmetal and leaded gunmetal. Via continuous casting technique, soundness of the continuous casted bar may be significantly increased. Flaws, defects will be unusual to spot if manufacturers adopt the technique.One of the great advantages of continuous casting technique is that the casted bar will be clean inside and out, which is beneficial for manufacturing tubes. In contrast to Chill Casting, continuous casting is preferred for its high productivity, consistent properties of materials and excellent production.
Strengths of HSIN HUAN LUNG MACHINERY INDUSTRIAL COMPANY (HHL)
-
Advanced, Efficient and Professional Equipment
HHL offers brilliant products with the most advanced High Frequency Induction Furnace, Vertical Centrifugal Machine, Horizontal Centrifugal Machine, Sand Preparation Equipment and Furan Equipment. With the constant introduction of high quality equipment, advanced technology and precision inspection instruments into our company, HHL presents products in the best quality.
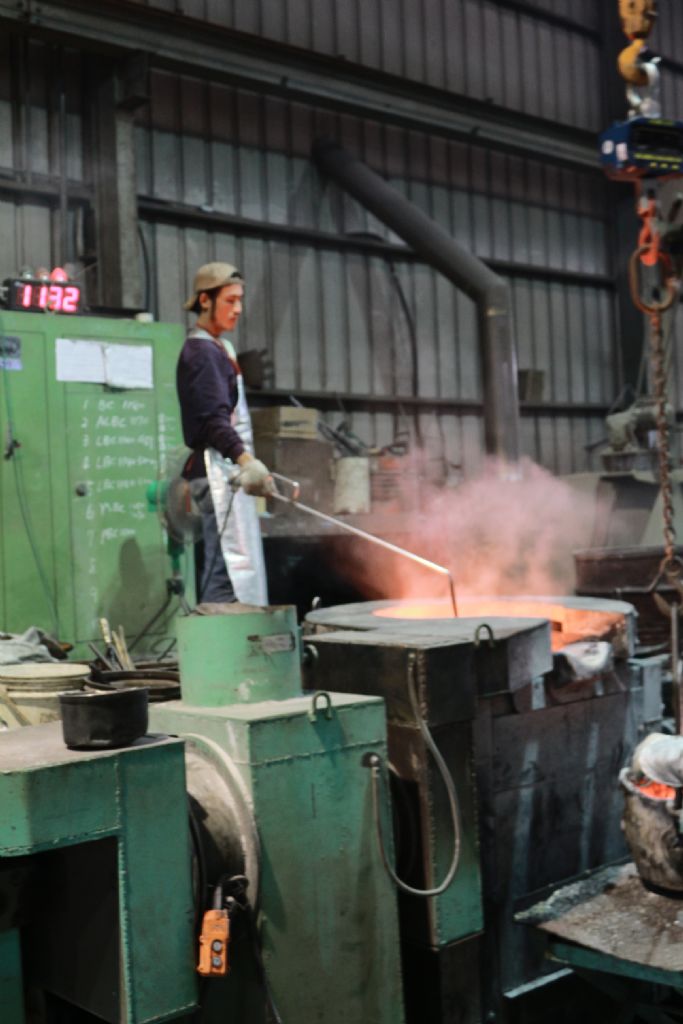
-
Various, Optional Casting Techniques
HHL provides 4 major casting techniques including Sand casting, Centrifugal Casting, Furfuryl Alcohol Casting and Permanent Mold Casting to meet your needs.
-
Flexible Centrifugal Casting Customization
Various kinds of materials, such as copper alloys, special steel and stainless steel are available. Contact HHL to get more details about feasible materials.
-
Mass Production to Small-batch Production
From mass production to small-batch production, we provide products that are dimensional, material customizable. Seeking tailored components? HHL is devoted to satisfying all your demands.
-
ISO 9001:2015 Qualified, Fulfills Your Needs:
Over the last thirty years, HHL assures our clients of high and stable quality. To serve our clients, we set up a Machining Department and cultivate our own professional machining team, so that we can provide high-quality finished machined components.
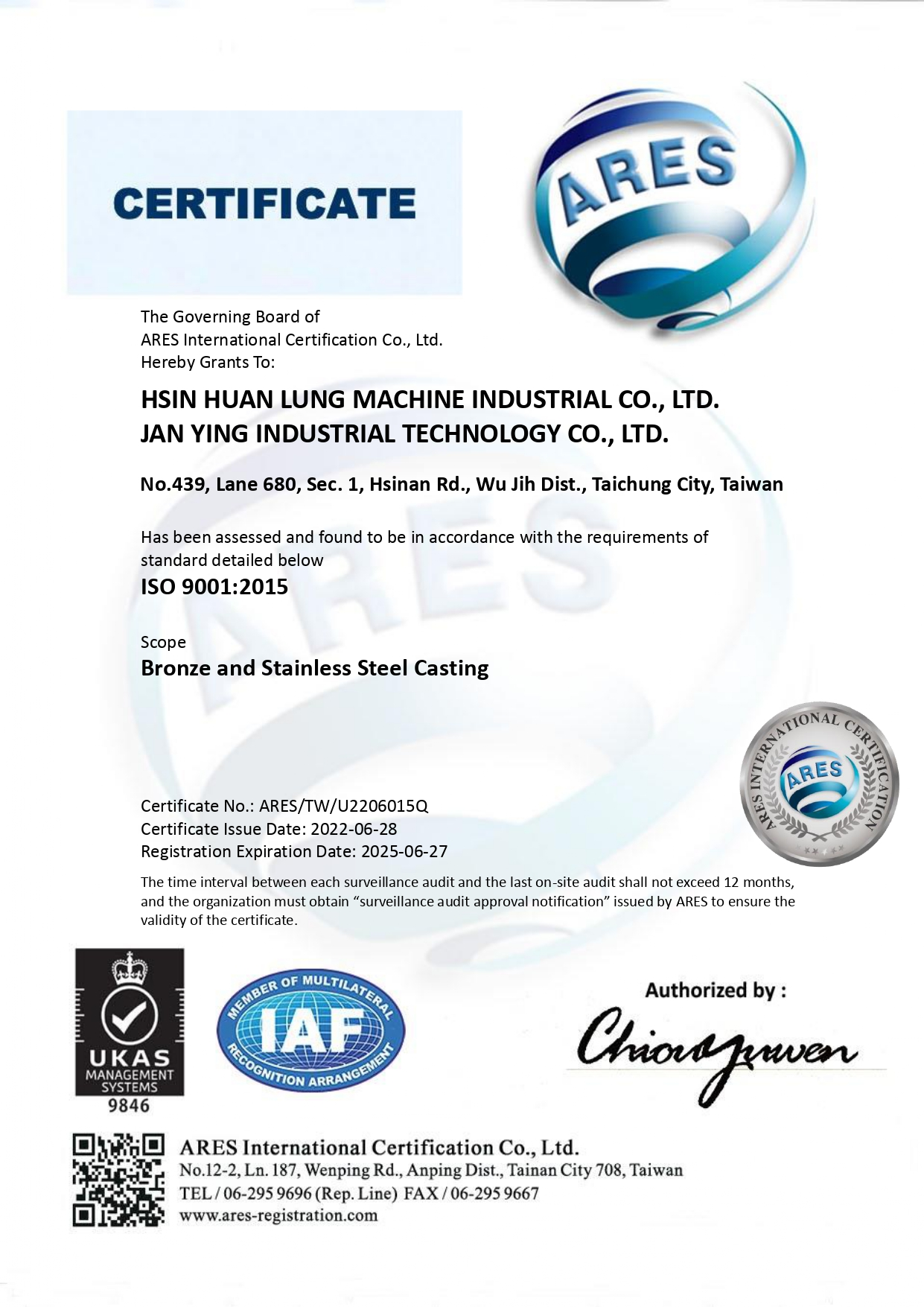
Contact HHL To Get a Satisfying Order
COPPER: 886-4-23350012STAINLESS STEEL: 886-4-23358196
FAX: 886-4-23350006
MAIL: hhl.sales1@gmail.com
ADD: No. 439, Lane 680, Section 1, Xinan Road, Wuri District, Taichung City