What Is a Worm Gear?
A worm gear is a type of gear consisting of a worm or screw-like gear, which meshes with a gear wheel or a worm gear wheel. Worm gears are an essential type of gear mechanism that is used in many industries and applications. Known for their ability to transmit high torque and power, Worm gears make them an ideal choice for applications that require high precision and efficiency.In this article, we will discuss what worm gears are, features they possess, the applications of worm gears and the metallurgy of worm gears.

Table of Contents
What are Worm Gears?
Before explaining what worm gears are, let’s talk about the components of worm gears. Worm gears consist of a worm or screw-like gear and a worm gear wheel. With a helical groove on its surface, which looks like a screw.The worm gear wheel, on the other hand, is a type of gear with teeth that mesh with the worm gear.Worm gears, namely the combination of a worm and a worm gear wheel, one of the gear mechanisms that is usually used to drive gear, while the worm gear wheel is the driven gear. The driving gear rotates the worm gear, which in turn rotates the worm gear wheel. Worm gears are known for their ability to transmit high torque and power, making them an ideal choice for many industrial applications.
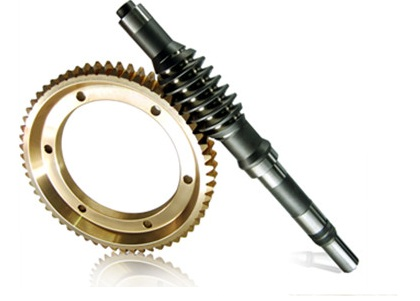
Worm gears come in a variety of types, each with its unique advantages and disadvantages. Some of the common types of worm gears are:
Single-Enveloping Worm Gears
In single-enveloping worm gears, the worm wheel is a cylinder with a concave profile that engages with the worm. This type of gear provides high accuracy and torque transmission but has limited contact area, which can lead to high wear and noise levels.Double-Enveloping Worm Gears
Double-enveloping worm gears have two concave curves on the worm wheel, which provides a greater contact area and better load distribution than single-enveloping worm gears. This type of gear is more efficient and has lower noise levels than single-enveloping worm gears but is more expensive to manufacture.Non-throated worm gears
This type of worm gear has an offset design that allows for a larger gear size and increased load capacity. The worm is offset from the centerline of the gear's throat, resulting in a gear that has two distinct radii.Single-throated Worm Gears
Single-throated worm gear has a worm that engages with one side of the gear teeth, which results in a smaller size and lower load capacity than a double-enveloping worm gear. Single-throated worm gears are commonly used in various applications, particularly in situations where space is limited or a compact design is required.Double-throated Worm Gears
In a double-throated worm gear, the worm wheel has two separate throats, which are the spaces between the teeth. The worm gear has two teeth that are offset by 180 degrees, each of which engages with one of the throats. As the worm rotates, it engages with the teeth on the worm wheel, causing it to rotate in the opposite direction.Helical-worm Gears
This type of worm gear has a helical-shaped worm that engages with a helical-shaped gear, resulting in smoother operation and less noise than traditional straight-tooth worm gears. Nonetheless, in terms of reduced noise and smoother operation, they may not be the best choice for applications that require high efficiency, high speed ratios, or low manufacturing cost.Right-angle Worm Gears
In this type of worm gear, the worm is oriented at a 90-degree angle to the gear. This design allows for compact and space-saving applications, making it ideal for tight spaces and high-torque applications. However, they may not be the best choice for applications that require high efficiency, high torque capacity, or high speed ratios.Duplex Worm Gears
Duplex worm gears are a type of worm gear that consists of two worm gears mounted on a common shaft. Each worm gear is responsible for transmitting half of the total torque. This means that each gear is subjected to half the load of a single worm gear, resulting in reduced stress and wear on individual teeth. Additionally, the distance between the two worm gears helps to distribute the load more evenly and prevent excessive deformation.Each type of worm gear has its own advantages and disadvantages, and the choice depends on the specific application requirements. It is important to consider factors such as load capacity, efficiency, noise, space limitations, and cost when selecting the appropriate type of worm gear for a given application.
What are the Features of Worm and Worm Gears?

For starters, let’s talk about the features of worm gears. Worm gears have several features that make them unique and highly desirable for many industrial applications. One of the most notable features of worm gears is their ability to transmit high torque and power. Worm gears have a high gear ratio, referring to the ratio of the number of teeth on two gears that are meshed or connected together in a mechanical system that allows them to transmit a high amount of torque even at low speeds. This makes them ideal for applications that require high precision and efficiency, such as machine tools and robotics.
Another feature of worm gears is that they can operate quietly and smoothly. Worm gears have a high contact ratio ( the amount of tooth contact that occurs between two meshing gears as they rotate ) , which means that the worm gear wheel is always in contact with several teeth of the worm gear. This results in a smooth and even transfer of power, which reduces noise and vibration.
Worm gears are also known for their compact design, which is a design that minimizes the space required for a particular function or purpose. Worm gears have a small form factor, which makes them ideal for applications where space is limited. The compact design of worm gears also makes them easy to install and maintain.
Although worm gears have many advantages, they also have some limitations and potential drawbacks. Some of the flaws of worm gears. For instance, The sliding action between the worm and the gear can lead to wear and tear on the gear teeth. This may reduce the lifespan of the gear and increase maintenance requirements. Apart from that, Worm gears require adequate lubrication to operate smoothly and prevent excessive wear. However, improper lubrication can lead to increased friction and heat generation, causing damage to the gear.
Despite these limitations, worm gears remain a popular choice for many applications due to their high torque transmission capacity, compact size, and quiet operation. By understanding the limitations and potential drawbacks of worm gears, designers and engineers can select the appropriate gear type for their specific application requirements.
What are the Features Applying Worm Gears?
High Reduction Ratio
Worm gears can provide high gear reduction ratios in a compact and efficient design. This makes them ideal for applications where a high torque output is required.Smooth and Quiet Operation
The sliding action between the teeth of worm gears results in smooth and quiet operation, making them suitable for applications that require minimal noise and vibration.Self-locking
Worm gears are self-locking, meaning that they can hold their position without the need for a separate brake mechanism. This makes them ideal for applications where it is necessary to maintain a fixed position or prevent backdriving.High Shock Load Capacity
Worm gears have a high shock load capacity, which makes them suitable for applications that involve sudden or intermittent loads.High Reliability
Worm gears have a simple design with fewer components, which makes them more reliable and easier to maintain.Versatility
Worm gears can be used in a variety of applications, including automotive, marine, industrial and aerospace.What is the Metallurgy of Worm Gears?
The metallurgy of worm gears is an essential factor in determining their performance and longevity. Worm gears are typically made from a variety of materials, including steel, bronze, and plastic. The material used for the worm gear depends on the application and the required performance characteristics, including:
Steel
Steel is one of the most common materials used for worm gears. Steel worm gears are known for their high strength, durability, and resistance to wear and tear. Steel worm gears are also capable of operating at high temperatures, making them ideal for applications that require high performance under extreme conditions.Stainless Steel
With the advantages of steel, stainless steel is also a corrosion-resistant material that is often used in applications where the gear will be exposed to harsh environments or chemicals.Bronze
Bronze is a common material used for worm gears due to its high load capacity and wear resistance. It is often used in applications that require high-speed operation and low noise.Cast Iron
Cast iron is a durable and cost-effective material that is commonly used for worm gears in industrial applications. It has good wear resistance and is capable of handling high loads.Plastic
Plastic worm gears are also available and are becoming increasingly popular due to their low cost, low noise, and self-lubricating properties. Plastic worm gears are lightweight, making them ideal for applications that require low inertia. However, they have limited temperature and load capabilities and are not suitable for high-performance applications.Which Fields Suit the Applications of Worm Gear?
Worm gears are widely used in automotive, machine tools, robotics, and various industrial applications. Some of the most common applications of worm gears were elaborated as follow:Machine Tools
Worm gears are widely applied in machine tools, such as lathes, milling machines and grinding machines. Machine tools require high precision and efficiency making worm gears preferable for these applications due to their capability to transmit great torque and power with low backlash.Robotics
Worm gears are also broadly applied in robotics, where they provide precise control over motion and high torque transmission. As we mentioned in the previous paragraph, worm gears possess brilliant accuracy. Robotics demand precision and accuracy, and that’s what makes worm gears ideal for these applications due to their low backlash and capacity to provide precise control over motion.Automotive Machine
Worm gears are used in the automotive industry in applications such as steering systems and power transfer units. Worm gears are ideal for these applications because they are able to transmit high torque and power and their compact design.Marine Machine
Worm gears are also used in the marine industry in applications such as winches, hoists, and steering systems. Worm gears are ideal for marine applications due to their resistance to corrosion and ability to withstand high shock loads.Aerospace Machine
Worm gears are used in the aerospace industry in applications such as actuators and control systems. Worm gears are ideal for aerospace applications due to their capability to provide precise control over motion and their compact design.To sum up, worm gears are an essential type of gear mechanism that is used in various fields and industries. Worm gears provide high torque transmission, precise motion control, and quiet operation, making them preferable for applications that require high precision and efficiency.
HSIN HUAN LUNG (HHL) the Leading Worm Gear Manufacturer
HSIN HUAN LUNG is a manufacturer of worm gears that has been in business for over 20 years. We specialize in the design and production of precision worm gears, providing custom solutions to meet the needs of clients.High-quality Worm Gears
HHL is committed to delivering high-quality worm gears that meet or exceed industry standards. They use advanced manufacturing processes, state-of-the-art equipment, and high-quality materials to ensure the quality of their products.
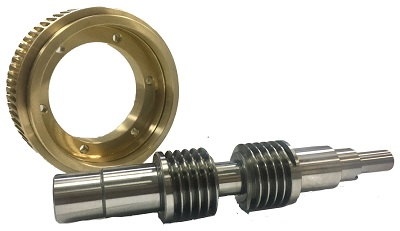
Experienced, Skilled and Professional
HHL builds a team of experienced engineers and technicians who are experts in worm gear design and manufacturing. The knowledge and skills we provide serving custom solutions that meet the unique needs and requirements of our clients.
Outstanding Customer Service
HHL is committed to providing excellent customer service to our clients. We work closely with our clients to understand the needs and requirements, providing support and guidance throughout the manufacturing process.
Reasonable Pricing
HHL offers competitive pricing for worm gears without compromising on quality. We work to provide cost-effective solutions that meet the needs and budgets of clients.
Tailored Customization
HHL provides custom solutions for worm gears. We work with our clients to design and manufacture worm gears that meet their specific needs and requirements.
Contact HHL To Get a Satisfying Order
COPPER: 886-4-23350012STAINLESS STEEL: 886-4-23358196
FAX: 886-4-23350006
MAIL: hhl.sales1@gmail.com
ADD: No. 439, Lane 680, Section 1, Xinan Road, Wuri District, Taichung City